SolidMill FreeForm™
Machine Complex Free-Form Shapes with Ease
ESPRIT's NURBS-based machining engine handles fabricating difficult free-form shapes with ease. Specifically designed to address the 3D challenges in the mold, die, and toolmaking markets, ESPRIT provides you with a powerful set of tools and machining cycles for free-form roughing, Z-level machining, finishing, and re-machining in 3-axis or 5-axis.
5-axis Free-Form Machining
Machining complex 3D parts in a single setup is easy with the powerful ESPRIT CAM system. ESPRIT streamlines programming and provides dynamic onscreen program verification, eliminating the need for expensive machine-tool dry runs. For 5-axis finishing, ESPRIT gives you a full range of options, including planar, normal, transitional, parametric, and offset styles. Program your 3D 5-axis machine cycles with ESPRIT and benefit from the superior surface quality, part accuracy, and material removal rates provided by today's multi-axis machine tools.
ProfitMilling
Learn more about High Speed Machining here.
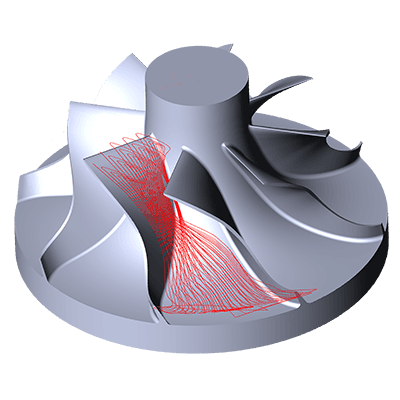
Roughing and Finishing for Complex Parts
Achieve high-quality surfaces with ease with ESPRIT's roughing and finishing cycles, with one- or two-tool options. ESPRIT's 3D roughing cycle performs zigzag, offset and spiral-style rough machining on even the most complex free-form solids and surfaces. Select from nine different semi-finishing and finishing cycles and machine your 3D workpiece to perfection — use one cycle for finishing the entire part, or define containment boundaries and machine zones differently using the most appropriate cycles and cutting styles for each.
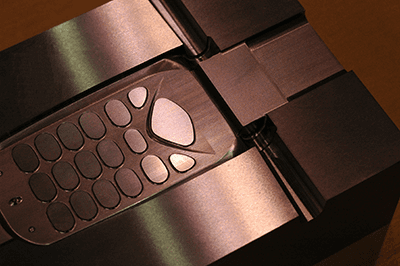
Z-Level Machining
ESPRIT's Z-level machining cycle automatically maintains constant loads on cutting tools for smooth, continuous high-speed toolpaths. When creating a Z-level finishing operation you have the option to machine the entire part or selectively machine only vertical or horizontal areas. When machining the entire part you can choose to cut the vertical and horizontal areas with different tools and use both roughing and finishing options.
Roughing and Finishing for Complex Parts
Achieve high-quality surfaces with ease with ESPRIT's roughing and finishing cycles, with one- or two-tool options. ESPRIT's 3D roughing cycle performs zigzag, offset and spiral-style rough machining on even the most complex free-form solids and surfaces. Select from nine different semi-finishing and finishing cycles and machine your 3D workpiece to perfection — use one cycle for finishing the entire part, or define containment boundaries and machine zones differently using the most appropriate cycles and cutting styles for each.
Automated Rest Material Re-Machining
Automate re-machining of the uncut areas of your part for maximized part quality and minimized bench work with ESPRIT's rest-material re-machining cycles. ESPRIT monitors the material left over from previous machining operations and uses the information to automatically perform any number of roughing and finishing cycles. Choose from pencil tracing, lace cutting, parallel flowline, and spiral tool-motion patterns, then select a cutter to automatically remove all remaining material.
Machine Regular and Irregular Workpieces
All ESPRIT free-form machining cycles are optimized for machining regular and irregular-shaped stock and workpieces including surface, solid and STL models, and previously machined workpieces. All cutting is identified and contained "limited to the material to be machined for the final part" resulting in optimized machining, reduced cutting time, elimination of air cutting and extended tool life.
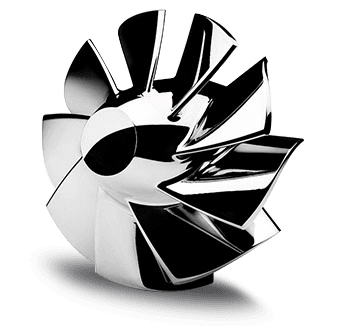
Simulation and Verification
See exactly what will happen at the machine before you ever cut a chip. View the entire machining environment, including stock materials, fixtures and clamps, in dynamic, solid-shaded graphics. All the kinematic action of your machine is displayed in "real time", giving you an incredibly accurate verification of the entire machining process. Using ESPRIT's built-in part inspection you can easily compare the original "as-designed" part to your "as-machined" workpiece to assure part accuracy. The realistic images let you see the part as if you were holding it in your hand.